Job shop scheduling best practices
Efficient job shop scheduling is no mean feat.
In fact, it's complicated enough to have inspired a term in the computer science world, "the job shop problem." We might say that, at its basis, the job shop problem is an issue of balancing sequences of actions with a limited number of resources to finish work in the most time-conscious way possible.
Sound familiar?
Unlike larger manufacturing facilities that produce a standardized set of high-volume consumer or industrial goods, job shops are required to be nimble and produce quality, short-run custom parts for their customers.
Shifting needs mean less opportunity for standardization and lean implementation than in larger operations, but there's still a lot you can do to make scheduling more efficient and responsive at your job shop.
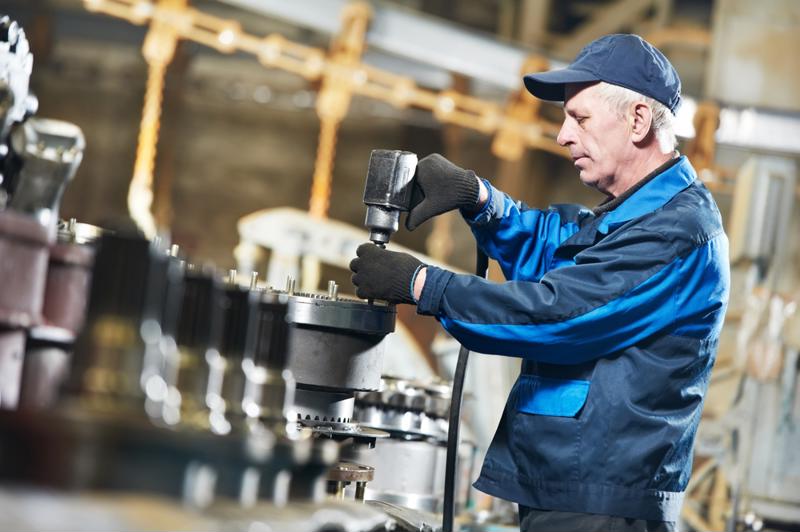
Job shop pressures
In addition to the small-batch, customized nature of the job shop, new, mounting pressures are putting strain on scheduling, and these issues need to be accounted for.
An article in the Fabricator pointed out that, "top-tier suppliers continue to push more functions down the supply chain, including inventory management."
Since they compete with comparable businesses largely on their ability to meet customer demands, and to do so on time, job shops have absorbed additional tasks, like inventory management, from their customers. This adds logistical complexity to an already challenging field. The article shares how job shops are now required to take care of forecasting duties.
Additionally, though job shop veterans anticipate that orders will be altered by the customer, a change in any one order or job has cascading effects for all other jobs being completed.
When you tweak the schedule for one job, you have to consider how it interacts with all other ongoing jobs and work in progress, as well as the equipment and staffing available.
What you should do to ease the pressure
Here are some strategies for more efficient, and adaptive, job shop scheduling.
Always be ready to change
The same Fabricator article mentions that it's easier to accommodate schedule changes when setup time is as a short as possible. They noted that the 5S methodology can help with this, as can investing strategically in updated equipment. You may still be able to retain older equipment for repetitive tasks that change little from one job to the next, requiring a minimal amount of resetting.
Enhance communication, transparency and integration
Manufacturing consultant Mark Stevens advised job shops to identify "barriers" like outdated data and poor cross-departmental communication. He also suggested keeping a closer eye on inventory.
If outdated information and siloed data across sectors of the job shop – and between the shop floor and the warehouse – are holding back your scheduling, you can do something about it. Keep your information up to date and accessible, and streamline communication.
Learn how Accent Software's ERP services can help you address pain points for your manufacturing operation today.